Regulatory Compliance
We not only know what to do but – how to do it.
We ensure that your quality systems are compliant with both the intent and spirit of FDA regulations.
Regulatory Compliance programs for life science manufacturers
How do you achieve compliance while managing your business needs?
Regulatory agencies demand that manufacturers maintain compliance throughout all stages of a product’s lifecycle, from concept to commercialization, including post-market compliance. The team of experts at BioTeknica, an IQVIA business, quickly integrates into your business processes, educating staff on current trends to minimize or eliminate downtime. Starting with a comprehensive gap analysis, enhancing your quality systems, and concluding with effectiveness checks, we achieve compliance while remaining sensitive to your bottom line.
Regulatory Compliance services:
Compliance Audits and Assessments
Third-Party Certification
Quality Systems Development and Remediation
483/Warning Letter/Consent Decree Resolution
Process and Product Quality Issue Resolution
cGMP Risk Analysis
Vendor & OEM Audits
ISO 9000 & EN 46000 Pre-Assessment Baseline Audits
Design Control Process Design and Implementation
Due Diligence Assessments
Agency Representation & Negotiation
Recalls, Field Corrections & Safety Alerts
Compliance Certification
Complaint Management & Reporting
Post Market Surveillance & Reporting
FDA 483 Responses
Corrective Action Programs & Management
Consent Decree Programs
Corporate or Multi-Facility Warning Letters
Monitoring of North American & European Union Regulatory Activities
Training & Education
Risk Analysis
Due Diligence Evaluations
We ensure that
your quality systems are compliant with both the intent and spirit of FDA regulations.
We are proud of our proven results and track record on behalf of both our smaller and larger multinational clients. Although every project presents unique challenges – the graphic below shows how we typically work together with clients.
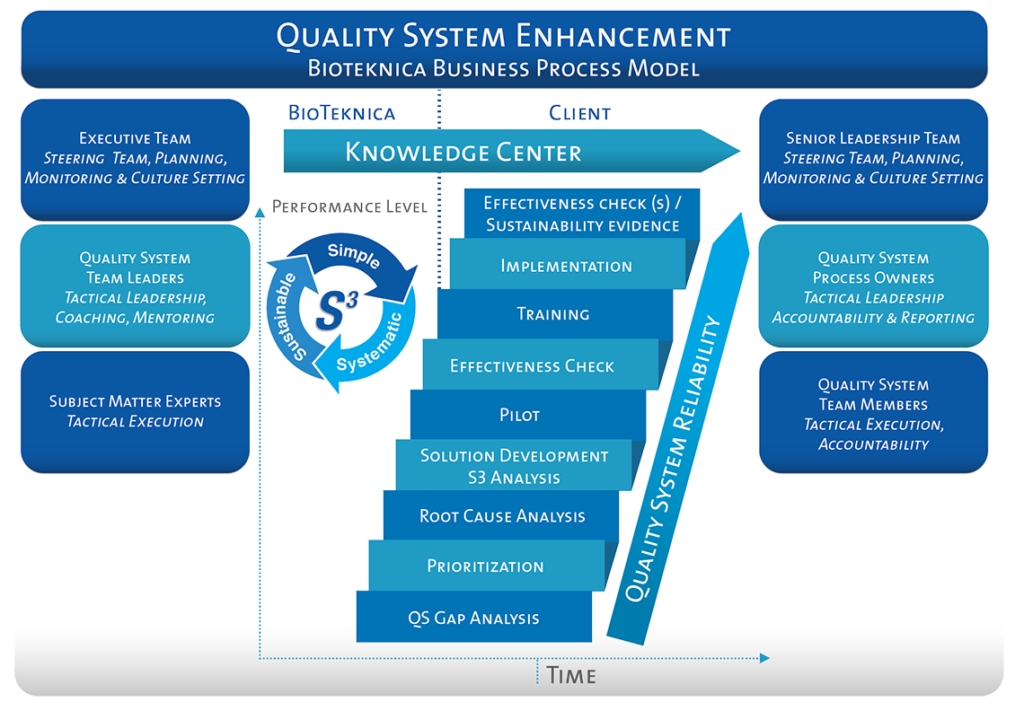
Our approach begins with a gap analysis and concludes with effectiveness checks. The foundation of our regulatory compliance work is Simple, Systematic, and Sustainable (S3) – methods that include experiential learning and ongoing improvement to quality systems. The chart also shows some of the key responsibilities that are shared and unique to the consulting and client teams.
Our regulatory compliance experts quickly integrate into your business process and educate your staff on current trends, thereby eliminating downtime.
1. Compliance Audits and Assessments
We conduct compliance audits and assessments. Our consultants have been on both sides of the table – we have industry and regulatory experience and:
- Understand what procedures are needed in today’s regulatory environment
- Determine how your quality systems elements relate to one another and identify the links between all the elements, e.g., between complaints and CAPA, between CAPA & risk management, etc.
While procedures may look relatively straightforward on paper – there are challenges to make them work together in a real-world environment.
- We know the latest trends. We’re up-to-date and current on the hot industry issues and trends. As a result, you benefit from the work we do with different types of clients, we fully understand the emerging issues and are able to help you deal with those issues – even before they become a challenge to your company.
- Conduct assessments based upon each individual client’s internal procedural requirements, e.g., utilizing your risk-rating scale, forms for recording observations, etc.
- Deliver all the necessary documentation while working within the framework of your internal audit system
- Partner with our clients to ensure that the solutions meet regulatory and business requirements
2. Third-Party Certification
We provide an independent assessment by industry experts who are:
- Experienced – we partner with our clients and their legal teams to ensure that the work is properly represented as part of formal, third party certification activities
- Knowledgeable – there is a tight wire you need to walk – one that accurately addresses both regulatory and business requirements. We know how to do that.
- Credibility – independent assessment by third-party industry experts needs to be approved by FDA
- Team players – we can work with your employees and other independent contractors to help you resolve issues and achieve compliance.
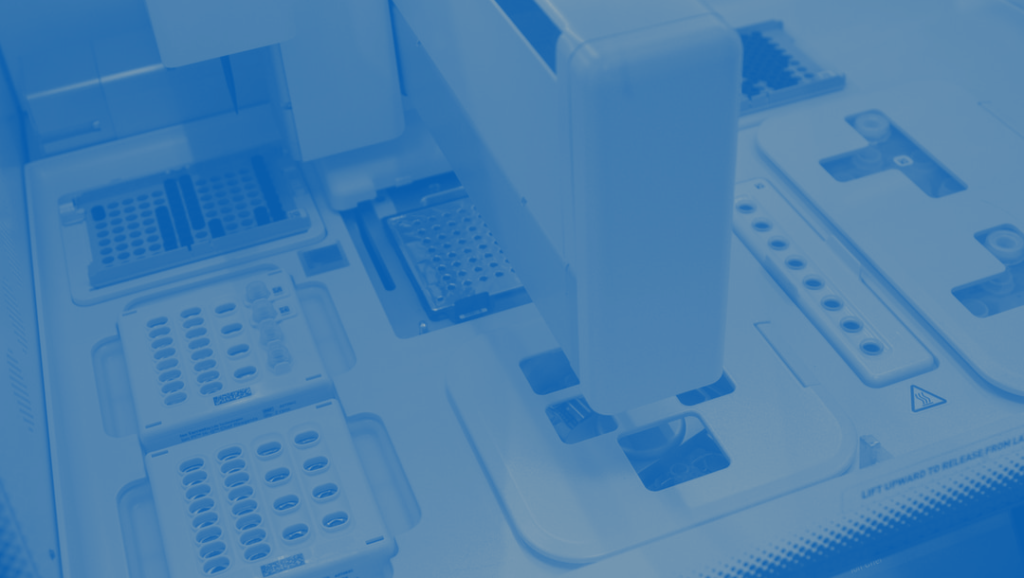
3. Quality System – Development and Implementation
- We customize your quality system as we partner with the process owners within your organization
- Understand the need to be compliant and meet your business requirements
- Leverage our knowledge of quality system best practices and our in-depth experience for your benefit; in other words, “we’ve been there and done that” – we have hands-on experience with similar companies and products, we customize that experience for you and hit the ground running.
- Work within the framework of your system; your staff learns using your own quality system
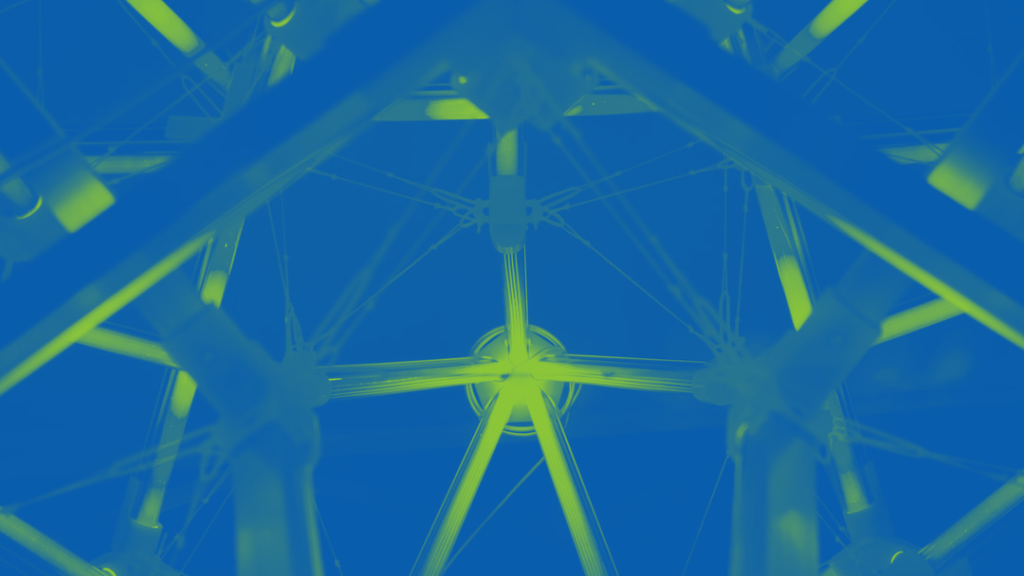
4. 483/Warning Letter/Consent Decree Resolution
- We identify the root cause(s) – a 483 is just a symptom of an underlying issue. Through years of experience, we understand that the issues typically lead far beyond what is actually written in the 483/warning letter. To truly resolve all the issues, we get to the root causes. A root cause may be a procedural process or educational/experience related; we identify and diagnose all the root causes and fill in the gaps.
- Possess the know-how you need – FDA regulations tell you what to do – but not how to do it. We not only know WHAT to do but – HOW to do it.
- Create win-win solutions – with our approach and methodologies, you receive quality system solutions designed to meet your specific needs. Our solutions not only meet FDA regulatory requirements – but are practical systems that your team can implement. By contrast, some regulatory consultants provide answers that may meet an FDA investigator’s needs but do not provide fully functional quality systems for your company.
- Provide Simple, Systematic, Sustainable S3 Solutions – How do you convey to the FDA that your team can really carry out your quality system consistently, on an ongoing basis? Our team can help with experiential learning… clients also benefit from our Inspection Readiness services.
- Employ proven methodologies – for the assessment and diagnosis of root causes and solution development, we use six-sigma, Kepner-Tregoe, etc.
- Provide comprehensive solutions – quality system assessment, development, and implementation activities can be done within the site quality system requirements such as CAPA, internal audits, quality planning, etc. This ensures that the FDA investigator understands that you have fully resolved issues within your quality system.
- Share the same goals – SAFETY and EFFECTIVENESS – your products need to be safe and effective for your customers, health providers, and patients.